The adoption of Internet of Things has grown in the retail world since I last wrote about it in December 2013. While larger companies are benefitting from this technology, many smaller merchants are not sure if it can help them. This post helps clear some of these doubts.
Internet of Things — IoT — refers to a network of connected devices that can communicate with each other, and can also be remotely accessed via a wireless connection using Wi-Fi or cell phone networks. A good example is a vehicle or a device that can be remotely accessed to track location. This is a one-way transmission of data — i.e., a user sending a request to check the location of a car or a device.
The process becomes more useful with two-way communication, when a device senses something and then sends data. As an example, a car could alert the owner if someone is trying to break in by deploying a sensor to detect broken window. This two-way communication is the primary reason for the increased adoption of IoT.
Retailers have been using one type of sensor, radio frequency identification, or RFID, in their warehouses for monitoring inventory for several years. RFID is also used in brick-and-mortar stores for a variety of purposes like smart labeling, which can detect theft.
With costs for a single tag, or sensor, coming down to around 5 cents, more retailers are adopting these solutions in their environment. It is beneficial and makes economic sense to do so. These tags are very small, as shown in the picture below, which makes them easy to deploy. They often have adhesive backing to easily attach to labels. They typically have a small built-in battery that can last up to three years, more than sufficient for tagging a single item but also enables reuse of the tag.
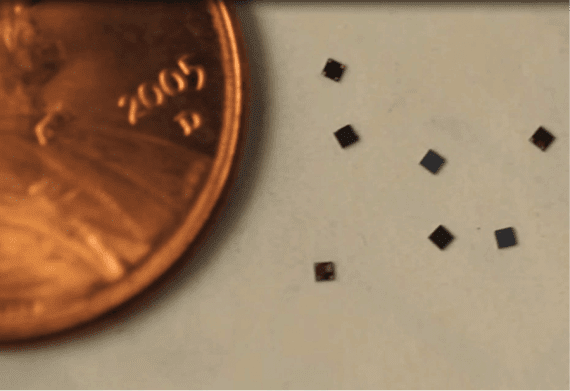
RFID chips are very small, the fraction of the size of a penny. Courtesy: Alien Technologies.
IoT for Inventory Management
Let’s use an example to illustrate. Say a retailer has $5 million in annual revenue with $1 million of inventory in its warehouse at any given time. This inventory consists of 10,000 items. Assume the retailer incurs an annual inventory loss of 0.10 percent, or $1,000. Each item deployed with a $.05 RFID tag will cost the retailer $500 — 10,000 items times $.05 each.
This expense can easily recovered by reducing the losses. The RFID tag can send an alert when an item is removed — i.e., stolen or lost — from the warehouse. The tag can also increase efficiency in the warehouse, as it can enable better inventory tracking and improve the order picking process.
Other IoT Sensors
Retailers can use other sensors beyond RFID to improve operations. There can be temperature-monitoring sensors to check the optimal temperature for perishable products and send alerts when necessary. There can be sensors that monitor the forklifts in the warehouse for predictive maintenance to avoid loss of productivity. There can be sensors in delivery trucks to monitor the deliveries in real-time, reduce losses, and make the delivery routes more efficient. Each sensor has a unique identifier to make it easy to determine the source and take action accordingly.
Getting Started
Utilizing IoT requires hardware and software. Many vendors — Softweb Solutions, Zebra, Novotech, Xively, SST — now offer end-to-end solutions. These vendors will work with a merchant to understand its needs and then define the type of sensors and software required to implement the solution. This will involve procuring the sensors and deploying them and the software. There are also vendors that sell cloud-based software, thus eliminating the complexities for an on-premise setup.